Where Should Water Come Out On An Outboard Motor
- Where Should Water Come Out On An Outboard Motor Video
- Where Should Water Come Out On An Outboard Motor Car
Jun 18, 2005 Does water come out of the exhaust. Discussion in 'Powerboats' started by midtower, May 29. Water should come out of the prop hub with the exhaust. I would take it back to the shop that worked on it last, they goofed something up, or your water pump has gone bad. I did remove both exhaust manifold hose's on the front of the engine.
The water pump impeller of any outboard motor needs to be serviced on a regular basis, a task that if overlooked can lead to big trouble. Most outboard maintenance schedules call for inspection of the impeller every 100 hours, or once a year. And once you’ve paid a tech to drop the gearcase and look at the impeller, you might as well spend another $25 and get a new one installed. The entire job is about $100 of cheap insurance.
The torn-up blades of this inboard impeller are not going to move much water.
- Re: Water coming out of exhaust on 1999 50HP The exhaust ports just above the water line should expel a combination of exhaust gases and water. The two mix in the outboard design (below the power head) to help keep things cool.
- How soon after starting engine should water start spitting out? I was told that you can run motor at idle with hose connected to. Without the tape the water is just draining pass the water pump and coming out the lower unit.
The impeller itself is simply a series of rubber vanes molded around a hub. The vanes are flexible, and the hub rotates on an eccentric within the pump housing, which has a stainless steel liner. The tips of the impeller vanes can wear out from simple use, but if the motor is often run in silty or sandy conditions, this abrasive material can accelerate impeller wear. The rubber material can also get stiff and brittle, a common problem on motors that sit unused for several seasons. Then the vanes can “take a set” in one position and not flex back. The other impeller-killer is heat. Water lubricates the pump, and if it’s run dry the impeller can be ruined in just seconds.
Note I said impeller service requires “dropping the gearcase.” For most of us checking the impeller is not a do-it-yourself project, which is probably why so many impellers are neglected until they fail.
“I think the most-common cause of impeller failure I see is simply old age,” says Dan Jansen, the lead certified Mercury technician at Mr. Marine in Fond du Lac, Wis. “Even with our short season, I find a lot of impellers that are too worn at the tips to pump well, or are really stiff. We make changing the impeller part of our off-season lay-up program, because if it fails you can have much more expensive problems.”
This Mercury outboard water pump was run dry briefly, and the impeller literally melted within the housing. You can see the imprint of the impeller on the back. In this case the entire water pump was replaced.
When the impeller fails, the pump can’t pump and the engine will overheat. I’ve seen old outboards that got so hot the paint burned off the powerhead. Most newer motors have a warning horn that sounds when the motor gets hot, and a program that cuts engine rpm to try and protect the powerhead, but Jansen thinks that often may be too little, too late.
“If they are running wide-open, by the time they hear that horn and react, they have a scuffed piston, especially if it’s a two-stroke motor,” said Jansen, “ And even if the motor is OK, now they are out in the middle of the lake and the day is shot, at the very least.”
A ruined impeller can also be caused by running aground, says David Greenwood, product planning manager at Suzuki Marine.
“You can suck a lot of abrasive trash into the pump if you run the gearcase into a sand bar,” says Greenwood. “I’ve seen cases where the water intakes were just packed to the point that water could not even get to the pump. If you get in that situation, it’s a good idea to have the impeller checked just as a precaution.”
The impeller to the right is new. The two to the left are old, with vanes that are worn, hard and curled over from sitting idle for years in an older motor.
Jansen and Greenwood agree that starting the engine “dry,” that is, with no water supply to the pump, is instant death to the impeller.
“A few years ago Suzuki actually did a study to see how long an impeller would last if you started the motor dry,” said Greenwood, “and it was about 20 or 30 seconds.”
Jansen showed me a Mercury outboard water pump housing he removed this season that is coated with melted rubber (see photo #2, above).
“The boat owner says he doesn’t know what happened, but I know he started the motor in his driveway, just because he likes to hear that two-stroke bark,” said Jansen. “This one got so hot you can see the stainless steel liner has actually recessed a little into the housing. The whole thing was melting.”
Where Should Water Come Out On An Outboard Motor Video
Greenwood says he’s seen boat owners who give the motor a quick bump with the starter on the launch ramp, just to make sure it’s ready to go when they get in the water, and others who think they need to start the motor after pulling the boat out of the water to drain it. Both are big mistakes that will ruin the impeller.

“Another issue is owners think they can start the motor if a hose is hooked up to the flush port,” says Greenwood. “That pushes water through the powerhead and exhaust, but very little gets to the pump. We tell owners to always use a set of water muffs on the gearcase if they want to start the motor with the boat on a trailer.”
If an impeller fails dramatically, simply installing new parts may not be the end of your trouble.
“If the impeller really comes apart, there’s a good chance that little bits of rubber can get lodged in the water tube and restrict flow to the powerhead,” says Greenwood. “You might notice a weak stream from the water pilot out the side of the motor, and that could mean that the technician did not check for impeller debris. If that’s uncorrected, the motor could overheat.”
You’ve been warned. Replace that impeller at the end of this season.
Charles Plueddeman is Boats.com's outboard, trailer, and PWC expert. He is a former editor at Boating
Where Should Water Come Out On An Outboard Motor Car
Magazine and contributor to many national publications since 1986.Article and Photos by Mark Corke
This is a fairly simple job, and the average do-it-yourselfer most likely has the necessary tools. Here's how it's done.
Ask around at the marina, and chances are that most boat owners have no idea when the water pump on their outboard was last serviced. Some people don't even know that their engines have pumps. The water pump is a critical part of any outboard. A pump that is blocked or working improperly will cause the engine to overheat, which can lead to permanent damage. If you suspect that the outboard is running hot, it could be time to service the water pump. The manual should say how often this should be done, but often every other year is about right. In most cases, this basically consists of replacing the water-pump impeller. Don't try to do this with the boat in the water. Have it hauled if it's large, or do the work when it's on the trailer in the driveway. That way, you won't lose anything vital.
The engine we serviced for this story is a 115-hp, 1996 Mercury. Outboards are very similar and, although the pictures might not look exactly like what you have, the sequence should be the same. You should, however, check the service manual for your own outboard because some are different from the one featured here. I took the pictures as Adam Conte at Portside Marine in Danvers, Massachusetts, serviced the pump.
1. The first step is to drain the oil from the gearbox. Unscrew the drain plug with a large screwdriver, and the oil will start to run out. Place a suitable pan under the engine to catch the old oil. Unscrew the upper oil-level plug, too, which allows air into the gearbox and ensures that all of the oil is evacuated.
2. There are small washers under each screw head that often get stuck in the threads. If they don't come off with the screw, you may have to pick them out with a small screwdriver or other tool. Let the oil drain as you move on to the next step.
3. Loosen and remove the nuts that hold the lower unit in place. Almost every outboard has four nuts holding it. A socket may not fit, so use a ring wrench to give good purchase on the nuts, which probably will be difficult to loosen.
4. Theoretically, the lower unit should now be free; in practice, it invariably sticks and will need a few taps with a soft mallet. Do not hit the flange cavitation plates at the sides or they're sure to break. A few taps on the aft end of the gearbox unit, as shown here, is acceptable. With some outboards, disconnecting the shift rod will require different steps. For example, you may need to unbolt the shift rod connection, then re-bolt it after the job.
5. Once a crack opens up, the battle is won, and you can carefully insert a broad screwdriver and carefully pry it apart, being very careful not to damage the castings of the mating surfaces. Lift the unit clear and place it on a suitable bench or jig designed for holding it. Portside Marine services outboards every day, so it had a proper jig. That's ideal, but you may have to prop the unit upright in the corner of your garage. It works but is just not as convenient, and you'll be working at floor level.
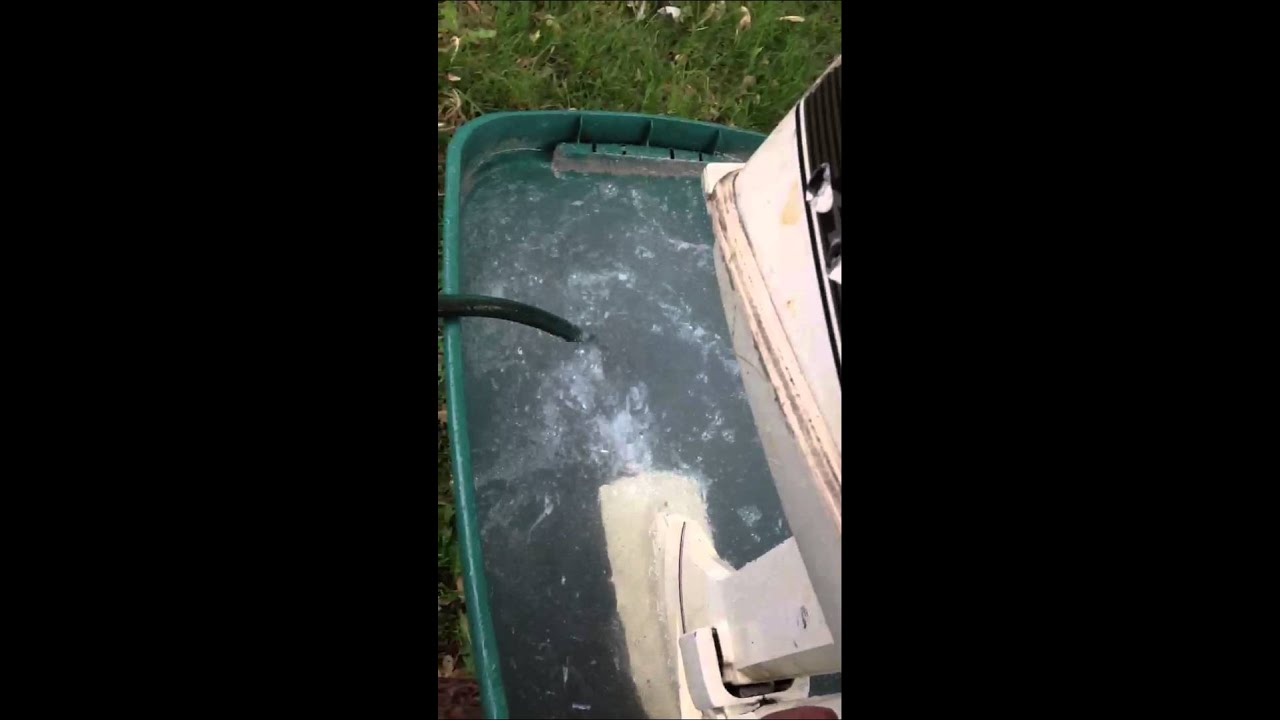
6. With the bottom clear of the top half of the lower unit, you can get to work on the pump. The first thing to do is slide off the seal, which sits atop the pump housing.
7. Unscrew the bolts that hold the pump housing in place. We needed an impact wrench because this pump hadn't been serviced for some time, but a ring wrench will work in most cases. Avoid using an open-ended wrench. If you round over the bolt heads, you'll have a bad day, for sure.
8. Separate the housing and slide it up the shaft. You can see in this picture that the bottom plate is coming off with it. We need to remove this plate, so if it remains stuck in place you might need to pry it up carefully.
9. This pump was in pretty good shape. All of the vanes on the impeller were intact. Note the old impeller on the right, compared to the new one and its straight vanes. The vanes develop a set (or bend) after they've been in the pump for several months.
10. Before reinstalling the pump, clean all of the mating surfaces to ensure that there will be no leaks. A sharp razor blade can be used to scrape off the larger bits of gasket and sealant; some fine emery paper will get rid of the remainder. Wipe with clean rags when you're finished. Everything should be clean and bright.
11. Wipe out the interior of the pump housing, making sure there are no score marks or gouges. If there are, water might leak past the vanes of the impeller and the pump won't work as efficiently as it should. If there is any doubt about the condition of the housing, replace it.
12. In addition to the impeller, all the required parts for routine service — gaskets, O-rings, seals — are included in the water-pump kit.
13. After cleaning everything, reassemble with the new parts. Smear on a little gasket cement. Conte, at Portside Marine, swears by Permatex Form-A-Gasket sealant, but other reputable brands should be fine.
14. Lower the gasket into position, making sure that all of the holes line up. The gasket is asymmetrical, so if something looks wrong you may have it upside down.
15. Install the new bottom plate that comes in the pump kit. We used a little more gasket sealant before dropping this on.
16. Install the smaller gasket, which seals the joint between the top and bottom sections of the pump housing. This gasket has a neoprene bead built in, so no cement should be used.
17. Install the new key, which sits in the flat on the shaft.Easeus data recovery wizard 11 serial.
18. Slide down the new impeller, making sure that the keyway in the hub lines up with the previously fitted key.
19. A little glycerin or dishwashing liquid makes getting the pump cover on a bit easier and provides lubrication for the second or two before the water gets into the pump and lubricates the vanes. Don't use oil or silicone, which can attack the composition of the impeller and lead to premature failure.
20. Slide the housing down and ease it over the vanes as you twist the shaft in a clockwise direction with the other hand. This bends the blades and allows the body of the pump to sit fully down onto the base plate gasket.
21. Reinstall the bolts and tighten until they're just snug.
22. Slide the new seal down over the shaft until it just rests against the pump housing.
23. Push the setting tool, included in the kit, down on top of the seal, which does the double duty of spreading it out and ensuring that it is not compressed too much. With the seal set, remove the compression tool.
24. Smear a little engine spline coupling grease on the top of the drive shaft.
25. Put a little more grease on the gear-shift coupler, which should still be on the gear shift shaft inside the leg. This is a fairly loose push fit, so the coupler may have fallen onto the floor if it isn't where it should be.
26. Refill the gearbox with the correct oil. Note that the oil is pumped in from the bottom until it comes out of the upper-level hole. Then both screw plugs can be replaced with a new washer under each. Portside Marine services a lot of engines, so it has a big tub of oil. The average DIYer is more likely to use the oil that comes in squeezable quart bottles, but the technique is the same.
27. Reinstall the lower unit. It helps to have someone rotate the engine by hand a little to get the splines to mesh. Replace the nuts and washers that hold the two parts together. There are torque settings for these, but Conte tightens them so they're just snug. As long as you don't swing on the wrench, it is difficult to overtighten these. The service manual may list torque wrench settings, however.
28. With everything back together, the job is complete. We ran the engine in a barrel to make sure all was well. You can use muffs on the water pickup, but the pressure of the hose tends to force the water into the engine. Running it in a barrel ensures that the suction from the pump is correct. There should be a healthy spout of water coming out of the engine housing. Record the date and engine hours so next time you'll know exactly when the pump is due for servicing.
— Published: February/March 2017
Recommended Articles
Outboard Flushing, The Right Way
Salt and brackish water is a corrosive killer, so flushing every time after saltwater use is a must
Checking Compression On An Outboard Engine
A compression check can tell a lot about the health of your outboard engine
Replacing Outboard Engine Gearcase Lubricant
Changing your engine's lower-unit lube every fall is a necessity
Tech Support
Degree Of Difficulty
Tools and Materials:
- Water pump kit
- Gearbox oil
- Flat-head screwdrivers
- Oil pan
- Ring wrench
- soft mallet
- Impact wrench
- Razor blade
- Emery paper
- Clean rags
- Gasket cement/sealant
- Glycerin or dishwashing liquid
- Engine spline coupling grease
Time:
This project will take approximately 1 to 2 hours
Cost:
Will vary based on the engine: Ours cost $50
BoatUS Magazine Is A Benefit Of BoatUS Membership
Membership Also Provides:
- Subscription to the print version of BoatUS Magazine
- 4% back on purchases from West Marine stores or online at WestMarine.com
- Discounts on fuel, transient slips, repairs and more at over 1,000 businesses
- Deals on cruises, charters, car rentals, hotel stays and more ..
- All For Only $24 A Year!